By Gary Shawhan, Contributing Editor, The CHEMARK Consulting Group
No matter where you turn, the intrusion of metrics in business or into our daily lives is pervasive and can be found in some form almost everywhere. Metrics today impacts the products or services that are available to us as consumers. In business, metrics continue to carve-out an expanded role in management decision making.
Types of metrics
The traditional role of metrics, as a business management tool, has been in the analysis of internally generated data. These business metrics provide both historical and current information on the company financial performance and operational practices that are important to managing the business as well as guiding its future direction.
Transactional metrics, in contrast, mainly come from external data sources. They provide management with a view of their business as it relates to the impact of various elements of a value-chain on the company’s performance and its ability to be successful. Business metrics and transactional metrics are derived from quantitative data.
Performance metrics, in contrast, are mainly developed from qualitative information gathered from a combination or sources. Collectively, performance metrics provide a pattern of activity or comparative information that can be converted into meaningful analysis. The key difference with performance metrics is that the information needs to be developed through market research.
It is important that this information be current and reflects recent changes or trends in the marketplace. Especially in markets or under business conditions that involve dynamic change, a fresh assessment of the present business situation is critical to guiding a company’s business strategy going forward.
Business Metrics
Business metrics provide information that characterizes the overall financial and operational health of the business. In general, these metrics, applied to most all businesses, tell management how the company is performing in relation to the company’s business goals. In most cases the data is obtained from internally generated data sources. Among the many items included in this category are the following:
- Gross profit
- Sales revenue growth, growth rate
- COGS
- Inventory, Inventory turnovers
- Sales by product line, by region, by sales territory, etc.
- .. any many others
Transactional Metrics
Transactional metrics involve accessing data from external sources. Businesses that sell products or services directly or indirectly to individual consumers need to employ transactional metrics to stay competitive in today marketplace. The fact that real-time data can now be collected and analyzed has added to the level of accuracy that is attainable.
Transactional metrics utilize data that has been collected from the ultimate customer such as retail stores, warehouses, elements of the supply chain or from distribution channels. Through the application of analytics massive amounts of data can be brought into a central location (or data lake) and then analyzed.
Companies doing business in the consumer space use this information to adjust their sales, marketing, and promotional strategy on a frequently basis. As the volume, frequency, and geographic complexity of a particular business increases, the value of being able to obtain and track real-time data from external sources becomes increasingly important. Examples of transactional data elements include:
- Seasonal trends, geographic preferences
- Market channel variances
- Packaging type, appearance
- Labeling
- Pricing
- Brand image, corporate image shifts
- … and many other
Performance Metrics
Performance related issues, industry trends, and market drivers represent metrics that are much more qualitative in nature. For many businesses, these issues are as even more important to understand and characterize. This is especially true for businesses whose strategy and revenue streams are distanced from the individual consumer. This includes companies that manufacture and sell finished goods that are sold into specific market segments where specific levels of product performance are required or specified. It also applies to companies that have technology or processes which deliver a unique, differentiated level of performance to the customers.
Regardless of the specific business type, developing meaningful performance metrics represents is a challenge. Information is not available from internal accounting data or through analytics obtained from a variety of external sources. It needs to be gathered through market research. Metrics are then derived from a qualitative assessment of the information gathered Examples of information as targets for applying performance metrics include:
- Competitive landscape; SWOT analysis, geographic concentrations
- Market mapping by segment, technology, geography
- Growth projections in key markets segments based on technology
transitions and market drivers that are creating opportunities
- Environmental, regulatory, waste recycling
Market Categories and Metrics Applied to the Coatings Market
Figure 1 represents three major categories of market types within the coatings industry each of which has different requirements and needs for the use of metrics.
Figure 1: 3 Types of Business within the Coating Market
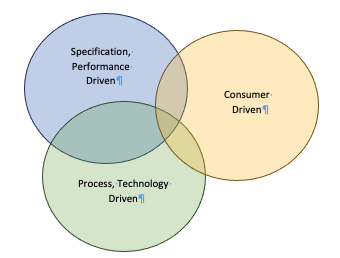
Consumer driven coating markets are ones that are closely aligned or have a direct link between revenue streams and the individual consumer. These markets are very dependent on market channels where the product choice or preference is often at or close to the point-of-purchase. Coatings sold through retail hardware stores, big box stores, regional or locally owned paint/hardware stores and internet sales represent a significant portion of this market category.
Consumer driven markets are characterized by the high importance placed on brand identity, company image, convenience, and the price paid by the buyer. Today, individual consumers are also increasingly sensitive to the suitability of products with respect to the environment, overall sustainability, and health and safety related issues associated with their use.
Metrics is an ideal tool for understanding consumer behavior and purchasing patterns. Sources of data from which analytics can be applied to evaluate a company’s current business are almost endless. Transactional data of various kinds, mainly obtained from external sources including retailers, distributors, etc., have become a necessary part of doing business in this space.
In addition to coating manufacturers, suppliers of resins and raw materials including pigments or additives need to have an active program to track various key metrics. This is a necessary part of staying competitive. Since consumer driven markets have a constrained value-chain for coating manufacturers (and their raw material suppliers) that limits profitability, metrics play a key role in strategic planning and business management.
Specification, Performance Driven markets, and the market forces that are important in determining business strategy for coatings are substantially different. The market drivers are normally dependent-on or aligned-with the OEM’s that represent the global leaders in a particular field. Automotive coatings represent the largest of these market areas. Other market examples include industrial and maintenance equipment, agricultural equipment, building and construction equipment, etc.
Specifications for individual equipment manufacturers can vary significantly depending in its application and type of service. In general, however, within a similar set of competitors, coating used is this market area reflect an established level of industry performance.
Metrics are important for Identifying and charting long-term trends in demand based on geography, climate and seasonal changes becomes very important. Tracking regional economic conditions in relation to sales and other end-use market statistics has become a key element in managing the coatings business in this area.
In addition, metrics related to import/export statistics, tariffs, and transportation costs are also key to managing this type of business. Most recently, supply-chain problems and the availability of parts to support global manufacturing of equipment has been added to this list.
Today, specification, performance driven markets are also affected by the issues related sustainability. OEMs are taking a proactive position in requiring their coating suppliers to provide next generation coatings that have a certain percentage of bio-based raw material content in them by a certain date. Metrics is a tool that can be used to benchmark competition and buying preference based on the value and revenue impact from having a proactive sustainability effort.
Process and technology driven coating markets are primarily associated with those markets where significant transitions are occurring or required to address changes in the product type, properties or form factor now being offered. These markets are very dynamics. In many cases, these markets have specific unmet needs which create opportunities for manufacturers to bring next generation product to market.
Metrics, applied to dynamic markets where process and/or technology change are a key to growth, focus on relevant trends in the marketplace. Identifying and tracking industry data that have been shown to precede a shift in technology or manufacturing processes is one example. Benchmarking against the established market leader or the key market challenger in a given field is another. More often than not these companies provide a bell whether for where the next generation of technology is headed or where these is an opportunity to capture share.
Alternatively, markets that have become commoditize can be considered within this category as well but with a significantly different set of market drivers. Commodity market have a very constrained value chain. Company’s look for different ways to gain an advantage over an established group of competitors.
Metrics, applied to commodity markets provide a means to monitor and manage manufacturing costs in relation to pricing in the marketplace. This analysis may extend to through the value-chain to develop a detailed understanding of the relevant strengths of various competitors in the marketplace. It can also identify potential role and impact of new technologies in a mature market situation.